PIM vs. PLM: What Is the Difference?
Welcome to another battle of acronyms! Who will come out on top: PIM or PLM?! Spoiler alert, ideally, they’d work together.
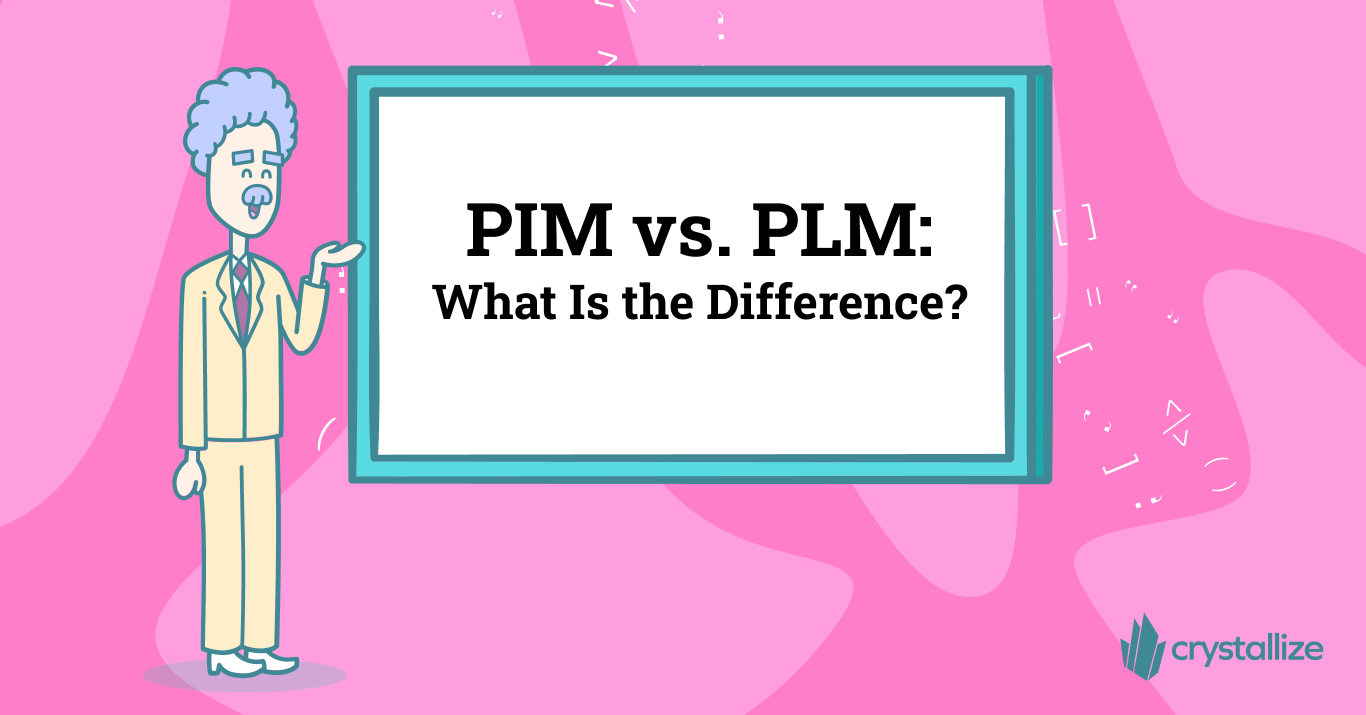
Product Information management (PIM) is focused on managing and organizing product data, while Product Lifecycle Management (PLM) is a more comprehensive system that manages the entire lifecycle of a product, from concept and design to retirement.
Together, they can streamline product management and improve overall business efficiency.
What is Product Lifecycle Management (PLM)?
Product Lifecycle Management (PLM) is a system or software used to manage the entire lifecycle of a product: it includes functions such as product data management, engineering collaboration, change and quality management, and supply chain management, among others.
Benefits of Using PLM Software
👍 Improves collaboration and communication by allowing teams to work together more efficiently by providing a centralized location for product data, where all team members can access, share, and update information in real-time.
👍 Increases efficiency and productivity by automating many of the manual processes involved in product development, such as data entry, version control, and change management, which can save time and reduce errors.
👍 By providing a comprehensive view of a product's lifecycle, the software enables managers to make informed decisions based on accurate, up-to-date data.
👍 Reduces costs by streamlining processes and improving efficiency
👍 Improved product quality by the enablement of management and tracking product data throughout the entire product development process, which can help to ensure that products are developed to meet customer requirements and comply with relevant regulations.
The Best PLM Software for 2023
- Siemens Teamcenter: This is a comprehensive PLM software solution that offers a wide range of features and capabilities and promises to connect people and processes across domains and departments and throughout the supply chain.
- Autodesk Vault: Designed for the manufacturing and construction industries, this solution also offers a range of features, including product data management, engineering collaboration, and change management.
- Aras Innovator: This is an open-source PLM software solution that offers a range of features and capabilities and is trusted by companies such as GE, Honda, Motorola, and XEROX, used in over 150 countries in the world.
💡Can Crystallize be used as PLM?
Depending on your use case, it will vary how good of a fit Crystallize is to manage the full product lifecycle. If you are retailing multiple product lines in multiple markets, directly or via a distribution channel, then Crystallize can be a great match, especially when these channels are webshops or Apps that are externally facing.
For example, you can create market-specific versions of your products and manage the specific lifecycle for the given product in the given market. Providing full control over the lifecycle of the various product versions.
You can also manage the timelines of when products should be made available for a specific market. All powered by the flexible product engine in Crystallize that enables limitless content modeling for your product data and information👇

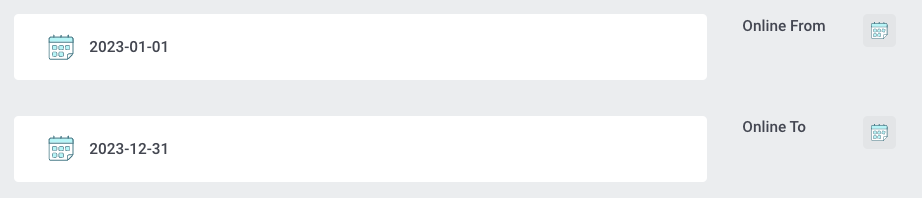
PIM vs. PLM: What Is the Difference?
As mentioned above, PIM and PLM both help improve product development and the management process, although from different perspectives.
PIM is primarily used to centrally manage, store, maintain, and distribute product information across an organization, mainly to help the sales and marketing departments, while PLM is used to manage the entire lifecycle of a product, from the initial concept and design stages to the retirement or end-of-life of the product.
📑Managing Product Data and Tools You May Need Infographic.
What is PIM, and how different is it from PLM? Where do PIM and DAM overlap? And do you need PXM for your business use case? We’ve tried to clear up the acronym confusion in eCommerce with the following infographic that provides you with a visual comparison of all relevant terms. Individual posts dig deeper into each term and the concept behind it.
📝READ WHAT IS PIM AND DOWNLOAD INFOGRAPHIC FOR FREE FROM HERE
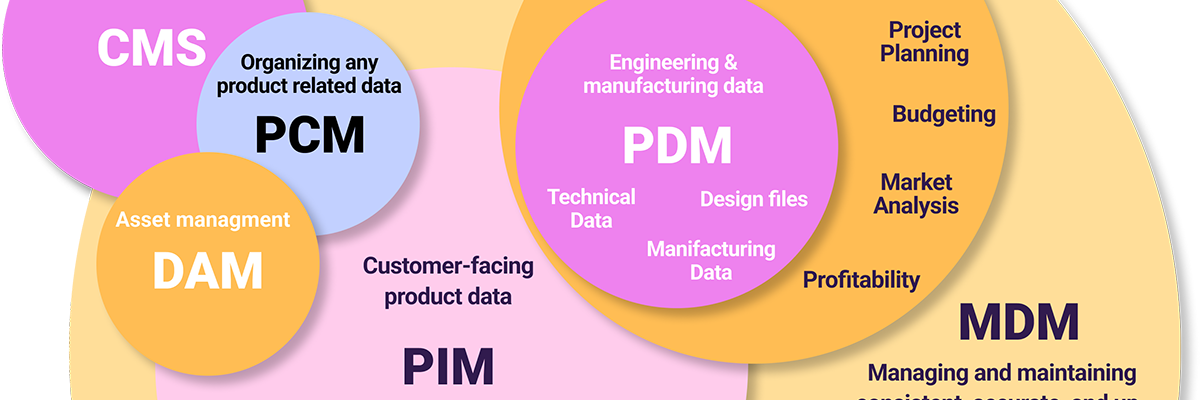
PLM Use Case
A wide range of industries would benefit from a PLM, but let’s say you’re an automotive manufacturer using a PLM to manage the development of a new car model.
The PLM system would be used to store and organize all of the data associated with the car's design, engineering, and manufacturing. This data would be accessible to all relevant teams, such as design, engineering, and manufacturing, in real-time. The PLM system would also be used to manage and track changes to the car's design throughout the development process. This ensures that all changes are properly approved, communicated, and implemented, which can help to minimize the risk of errors and delays.
Additionally, the PLM system can be used to manage the supply chain of the car's components, ensuring that materials, components, and sub-assemblies are available on time and within budget. This will allow the manufacturer to optimize the production and delivery schedule, reducing the risk of delays or stockouts.
Quality management tools within the PLM system would also ensure that the car meets all relevant industry standards and detect and correct issues early in the development process before they become expensive to fix.
Not sure if you need a PLM or PIM solution? Don't worry. We got you covered.
Seriously, schedule a personal 1-on-1 Crystallize demo, tailor-made to your use case, to understand the ins and outs of both approaches. Or, why not SIGN UP for FREE and get an unparalleled level of support from our team to help you get going.